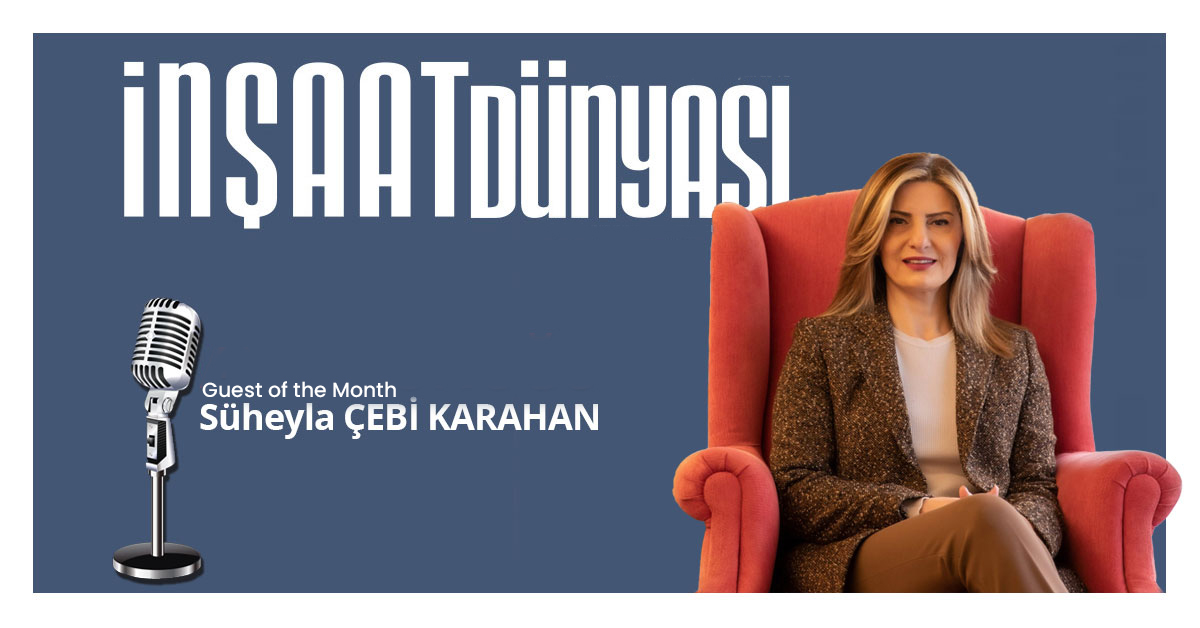
Prefabricated Modular Steel Structures Offer Numerous Advantages For The Construction Industry
“The prefabricated building market is expected to grow by more than 8 percent in the period 2020-2025, thanks to the positive effect of the factors such as; increase in infrastructure investments, recent developments in the housing sector and commercial areas, increasing middle-income population and rapid urbanization. In the light of these developments, consumers’ demand for longer-lasting, durable, comfortable and environmentally friendly buildings can be met with prefabricated steel houses, rather than traditional building system. As DORCE, we have an important brand value in the global market with our success in the prefabricated building production sector. We are the superstructure supplier for most of the newly built pandemic hospitals in Africa, the Middle East and South America. We continue our production processes without slowing down by closely following the changing economic conditions, increasing costs and new living conditions during the pandemic process. In our new roadmap, our growth strategy will be shaped in line with the digitalization strategic plan and its implementation, which is inevitable for our era. ”
SÜHEYLA ÇEBİ KARAHAN
CHAIRWOMAN
Can we listen to the story of DORCE, which is one of the strongest brands of both its birthplace and the global market with its production, export and international contracting activities?

DORCE is one of the leading and first established companies in the sector of prefabricated construction in Turkey. Our company, with 38 years of experience, complete the projects aimed at meeting all kinds of needs on a turnkey basis including engineering, procurement, production, logistics, assembly, infrastructure and superstructure works, testing and commissioning with all our own engineers. We stand out for the ability to operate in many different international regions with rapid mobilization under severe climatic conditions at same time. Today, DORCE’s factory, which operates with local and international quality standards, is Europe’s largest producer of light steel modular prefabricated buildings.
DORCE is the producer of Prefabricated Module Buildings, as well as the contractor who completes the turnkey construction of the products it produces, along with the logistics process. DORCE has proven itself in this field with both its manufacturer and contractor identity. Since DORÇE produces project-based turnkey solutions, has become a sought-after company with the motto “DORCE can where others cannot”.
The most important causes of why DORCE has the brand value in the Global market are the references after completed projects successfully, adaptation to different cultures, culture of partnership with local companies, ensuring the active participation of local subcontractors and suppliers of the construction process, the expert sent to the country where the project will be made from Turkey personnel and strong harmony between our Marketing, Business Development, Sales, Design, Purchasing, Production and Project Management Teams. We complete superstructures in all projects by exporting the International prefabricated modular steel construction elements produced in factories in Turkey. We are considered one of good industrialist and exporter company of Turkey.

How many countries does DORCE export to now? Which type of projects are you mainly preferred abroad?
Since its establishment, DORÇE has exported to more than 60 countries and has companies in 15 different countries. We export our products to 6 different countries even during the current pandemic period. We are preferred in foreign projects that require extensive organization, need to be done very quickly, simultaneously in different locations, or in challenging areas where we face material shortage. Worker Camps, Integrated Refugee Facilities, Military Camps and Military Bases, border camps, Schools, Dormitories, Hospitals, field hospitals, clinics, police stations, prisons, aircraft and helicopters in oil, gas and mining fields with a minimum capacity of 4,000 people and 100,000 people. hangars, ammunition depots, polygons, training centers, etc. These are the projects we mainly do as EPC (Engineering, Procurement, Construction). We are able to build steel armored bullet and mortar proof buildings that can be transported by air, and DORÇE is preferred for such special projects.
WE ARE THE SUPERSTRUCTURE SUPPLİER FOR MOST OF THE NEWLY BUİLT PANDEMİC HOSPİTALS
Can you give information about your recently completed, ongoing and upcoming projects? Which projects did you mainly take part in during the COVID-19 pandemic?
We have recently completed a quarantine hospital for 4,000 people in Qatar, military campuses for domestic and foreign defense ministries, and a 2,620-person accommodation facility in Kazakhstan. Currently we are working on Village Houses project for TOKİ (Housing Development Administration of Turkey), 9,500-person camp project in Mozambique, administrative building project for BP company in Georgia, domestic and foreign military projects, housing projects in Libya, 446 bed capacity hospital project continues in Iraq. Currently, Dorçe is the superstructure supplier for most of the newly built pandemic hospitals in Africa, the Middle East and South America.

What should we understand when it comes to prefabricated modular steel structure? Can you describe these structures in general terms from the material used to the method of construction?
When it comes to prefabricated modular steel structures, I think there is a confusion of concepts from the material used to the method of construction. Due to the technical terms I will try to explain the system in short lines as possible below. Internationally used terms and definitions express our business and our industry better. When we translate these terms into Turkish, sometimes they may not be correct expressions. Therefore, I will explain prefabricated modular building systems with Turkish and English definitions.
Offsite Construction; It means manufacturing, planning, designing and assembling building elements in a different location than their final installed location in order to support the rapid and efficient construction of a permanent structure. Such building elements can be prefabricated at a different location off site and transported to the site and then moved to their final location. Off-site construction is characterized by an integrated planning and supply chain optimization strategy.
Industrial Construction; is a building system that uses innovative techniques and processes and where structural components are manufactured in a factory then moved to the final location and assembled there. Industrial construction means that design and production processes are carried out by automation.

Prefabricated Structures; It is the practice of combining the components of a building in a factory or another production site and transporting all assemblies or sub-assemblies to the construction site where the structure will be placed. The term is used to distinguish this process from traditional construction method that takes place with the transfer of the main raw materials to the construction site.
Modular Structures; Completion of a building in a factory environment, ready-made, interior and exterior coating elements of the final connection lines such as sanitary and electrical installations, wall panels, roof, flooring, bathrooms, kitchen equipment, fully equipped with volumetric building modules that are shipped to the site. After the modules are transported to the field, they are ready to be used individually or in combination according to the intended use.
Modular buildings are a popular construction methodology in recent years, especially for education and healthcare structures such as hotels, schools and student dormitories. The main reasons for this are the particular benefit of the scale economy and reduced site construction time, which can be achieved with the production of many similarly sized modules. Broadly speaking, modular construction involves manufacturing the standardized components of a structure at an off-site factory and then assembling them on site. Terms such as “Off-Site Construction”, “Prefabrication” and “Modular Building” are used interchangeably. These terms cover a range of different approaches and systems, from single elements bonded together using standard connections and interfaces to fully furnished 3-dimensional volumetric units.

Volumetric Modular Structures; The success and appeal of volumetric module manufacturing lies in the repeatability of units and design. Volumetric modular units are large building elements that can be connected together to create complete buildings without the need for an additional superstructure. They are put into operation before leaving the factory. Thus we minimize non-conformities and ensure high quality control. The units are then transported to the construction site and carefully placed in their positions on the prepared foundations.
Panelized System Structures / Modular Panelized System Buildings / 2D Modular Buildings; panels are planar units surrounding the utilized space. These units can be uncladded (open panel) or cladded (closed panel), including windows, doors and / or other integrated services if needed. They are transported to the site in proper packs.
Hybrid Prefabrication / Hybrit Based Prefabrication / Half-Volumetric Prefabrication; It consists of a mixture of volumetric or modular units and non-volumetric or panel system units. It may also contain traditional field-made items. Hybrid structures generally use volumetric units for labor-intensive volumes such as kitchens and bathrooms (these units are also called “capsules or pods”), while the rest of the structure is built using a panel system.

Containerized Buildings; The term “containerized building” is often used to describe buildings created by using modules converted from freight containers used in shipping as building elements. However, volumetric modules produced in the factory in our country are also called ‘container buildings’.
Portable Structure / Portable Cabin; A demountable or portable building is a structure designed and built to be mobile rather than permanently placed. The smaller version of portable buildings are also known as portable cabins. Portable cabins are custom made prefabricated structures produced for various applications such as construction site office, security cabin, accommodation, warehouse, toilets. Portable cabins are an affordable alternative to traditional buildings and of course offer a flexible solution where temporary accommodation is required.
Flat Pack; It is the term given to units that provide transportation advantage by placing the walls and other elements forming the module obliquely between the ceiling and floor tiles. “Flat-Pack” units can be stacked on top of each other.

Pod / Capsule; The term pod or capsule is generally used for non-structural volumetric cabinets. They predominantly contain wet areas such as bathrooms, toilets and kitchens.
Light Gauge Steel Prefabricated Buildings / Building Systems; Light gauge steel building systems consist of structural frames produced using cold formed steel profiles. These frames or profiles can be used at all required points in a building, including load-bearing exterior and interior walls, non-load-bearing partition walls, floor beams, curtain walls, roof trusses and purlins.
Heavy Metal Prefabricated Buildings; They are modern construction products where the entire design is done in the factory and the building components are brought to the site as parts or sub-assembled and then fixed / assembled on site. It is generally preferred in structures where long span and height are important.

PREFABRICATED STEEL HOUSES ARE DURABLE, ECO-FRIENDLY, COMFORTABLE AND ECONOMIC
On the one hand, the increasing world population, on the other hand, the desire to live in longer-lasting, durable, comfortable and environmentally friendly buildings… In the face of this picture, does the construction with traditional building systems or the introduction of new models meet these demands?
Prefabricated building market will be positively affected and will grow significantly due to increase in infrastructure investments, developments in residential and commercial sectors, increasing middle-income population and rapid urbanization. Government-sponsored initiatives to provide affordable homes in a shorter time in developing countries will be another key factor influencing growth. In addition, due to the earthquake resistance of prefabricated buildings, it is likely to create demand from earthquake-prone countries. The increasing awareness of environment and construction waste around the world has led especially developed countries to eco-friendly policies and green building concept. We meet these demands by using prefabricated modular buildings instead of traditional building systems, the production of prefabricated steel houses in modern architecture with new generation construction methods and materials.

SUSTAINABLE STRUCTURES THAT MEET THE PRINCIPLES OF ENERGY EFFICIENCY AT A HIGH LEVEL
What kind of advantages does the use of prefabricated modular steel structures provide? Construction method, time, cost, occupational health and worker safety, seasonal effect, environmental awareness, durability, etc. What kind of differences do we see in these structures in terms of these factors?
While prefabricated modular steel structures meet energy efficiency principles at a high level, they also appear as sustainable structures. Prefabricated Modular building systems offer significant advantages through quality improvements as well as saving time and cost. Quality standards are high because the modules made in the factory are produced under controlled conditions before being transported to their location. If we list the numerous advantages of “prefabricated” steel structures for the construction industry today;
Lower Carbon Footprint – The Use of High Strength Structural Steels Reduces the Carbon Footprint: Prefabricated Modular Steel Buildings have a low carbon footprint due to reasons such as being pre-designed, construction in a shorter time and shorter equipment operating times. All materials used are recyclable and create less waste.

Ultimate Green Material Steel and Recycling: There are two ways a building can be considered “green”. The first is the way the materials help with operating costs, and the second is how the used materials reduce the environmental impact. Steel is one of the only building materials that can be recycled many times at the end of use without losing their strength. Dorçe uses light gauge steel components for the construction of modular structures. The recyclability of steel and all other materials used reduces the need to release more waste after use, and reduces the need for extraction for raw materials.
Eco-friendliness and Its Impact on Traffic: Another factor contributing to the sustainability of prefabricated modular steel buildings is that the majority of the prefabricated modular construction process is realized off-site. The negative impacts of the project on the environment and the site are significantly minimized. Thus, while the number of vehicles and heavy equipment needed in the field and their use decreases, gains such as less environmental pollution and increased occupational safety occur.
Earthquake Resistance: The steel system is an extremely resistant building system against earthquakes with its flexible structure, strength and lightness. Since prefabricated modular steel structures can be designed in accordance with the earthquake conditions of different regions, they perform better than other building systems when exposed to earthquakes. For these reasons, by improving the space perception of prefabricated modular steel structures in earthquake risk areas; Building with changes to be made in elements such as color, texture, material, light and shape should be considered as an option. As everyone says, destroyed buildings take lives, not earthquakes. While concrete buildings are collapsing during the earthquake, steel bends, deforms but does not break or collapse. Its collapse also means that the loss of life is reduced or even does not happen. After the earthquake, steel does not have to be demolished and rebuilt like reinforced concrete. It can be repaired and reused.

Shorter Construction Time: One of the most important advantages of prefabricated modular steel structures is that the construction can be completed in a shorter time than traditional construction methods. “What is Dorce doing?”, “What is Dorce’s greatest feature?” etc. Whenever they ask such questions, one of our answers is “We sell time”. Saving time, pre-planning production processes, eliminating adverse weather conditions that may occur in the field depending on the production carried out in the factory environment, and the production of different building elements or modules that make up the main building at the same time. Thus, the saving in time paves the way for rapid mobilization and undertaking of these projects in multiple projects in different geographies at the same time.
Financial Savings: Today, instead of traditional construction techniques, the use of prefabricated modular building elements is considered more advantageous than traditional construction buildings in terms of , cost control, high labor costs in developed countries, economic life of prefabricated steel structures, maintenance costs, recycling features, etc.
Safety and Security: Prefabricated modular structures provide important advantages to us when evaluated in terms of occupational safety and worker safety. Due to the production carried out in closed production facilities, the risks of occupational safety accidents decrease significantly. Strict follow-up processes and HSE procedures that protect workers and employees against injuries and accidents are applied within the scope of all production and assembly processes carried out in the factory environment. Work and worker safety is extremely important in construction sites where traditional construction methods are applied, but workers can be exposed to changing weather and ground conditions for a long time.

Climate conditions: Prefabricated modular steel structures can be produced in accordance with all seasonal conditions with current technologies and new materials. The interior insulation materials used in the buildings are selected in accordance with the climatic conditions of the geography where the project is carried out. For example, prefabricated modular steel structures designed and produced by Dorçe are durable and sustainable structures from -50 degrees in Siberia to +50 degrees in Africa.
Consistent quality: Since the prefabricated building takes place in a controlled manufacturing environment and follows the specified standards, the sub-assemblies of the building will be constructed in a uniform quality. The structures built on site depend on varying skill levels and schedules of independent contractors. All of these contribute to the craftsmanship and overall quality of the given structure. In prefabrication, each sub-assembly is built by an experienced team in the factory after multiple quality checks throughout the entire process.
Less People On-Site: Prefabricated and Modular building systems require less people for on-site installation. This is because these building systems are only assembled on-site, components are fabricated at the factory and are designed to fit together easily and therefore require less labor.
Plug & Play: It is a unique modular building system that allows a building to be entirely completed in the factory environment from the production to the final assembly, and the final connection lines such as sanitary and electrical installations can be sent to any region as one or several ‘modules’. Each module is built and shipped to the site, fully equipped with interior and exterior cladding elements, wall panels, roof, flooring, bathrooms, kitchen equipment, lighting. After the modules are shipped to the field, they are ready for immediate use, either alone or combined, depending on the intended use.

Portable, demountable and rebuildable structures: Prefabricated Modular Steel and modular structures are produced in the factory environment and shipped to the field. They are building systems that allow the use by demounting and assembling for reuse in different locations after the assembly is completed and used for the required period of time.
The prefabricated building market is expected to grow by over 8% in the period 2020-2025.
In which countries are prefabricated modular systems most used? What is the prevalence of these systems in our country? From this point of view, I would like to ask, how much share do prefabricated steel modular structures have in the market?
Countries that use the Prefabricated Modular Buildings most by region;
Middle East and Africa,North America (USA, Mexico and Canada),South America (Brazil),Europe, (Germany, England, Italy, France, Turkey)Asia Pacific (China, Malaysia, Japan, Philippines, Korea, Thailand, India, İndonesia and Australia)The prefabricated building market is expected to grow by over 8% in the period 2020-2025. The global modular construction market size is projected to reach 106.22 billion USD by 2027. Market depth is high in developed countries such as the USA and Western European countries. At the same time, the prefabricated building industry is just beginning to form in emerging economies such as China and India. Leading international prefab manufacturing firms are likely to increase their presence to get more shares, especially in fast developing countries in Asia-Pacific and Latin America. There are many technology-based prefabricated modular building manufacturing companies across the USA, Japan, China and Europe. They are very successful in automation, engineering, trade and production.
While technological developments continue to transform all sectors, companies build their business models through digitalization. Can we learn about DORCE’s investments and works in this field?
In order to increase the use of artificial intelligence programs that we have initiated in the company, we provide training to the personnel with video conferences, we plan to accelerate the information sharing between departments with artificial intelligence programs and to sell our products through digital platforms. While updating our existing ERP system with new advanced versions suitable for our era, we also install the BIM system. We also established a Digital Marketing Department, and we are doing our product promotions and business development almost entirely in digital environments.

A CONSTRUCTION SECTOR INTEGRATED THROUGH ARTIFICIAL INTELLIGENCE WILL WORK MUCH MORE EFFICIENTLY
With the increasing role of technology-based systems, how do you foresee the speed of digitalization that will change the future of the construction industry?
In this era of rapid technological developments and digitalization, many large companies in the construction sector are investigating how to apply digital developments to their firm structure. My foresight is that a construction sector integrated with artificial intelligence programs in project design, supply chain, logistics, product and quality management will increase the quality of work while working much more efficiently. Many companies that trade with each other in the world will integrate with each other through artificial intelligence programs and will shorten the project and business planning times.
How has the pandemic process reflected on your work in the domestic market and abroad? What are the problems created by the process?
During the pandemic period, the works of the construction companies exporting and continuing their projects abroad were delayed, stopped or partially continued. Among the reasons for these are quarantine practices, travel and customs restrictions, prolongation of logistics times, and rotational work of the staff at the ports. During the pandemic, as DORCE, due to the nature of our business, we took the necessary measures by taking action very quickly. Despite the travel restrictions, the management team in the fields where DORCE does business continued to work in the regions where they were assigned, and continued the continuity of our projects without interrupting the local workforce network. We obtained the COVID-19 Safe Production Certificate by complying with the local regulations for our head office, construction sites and production facilities. We continued our production processes without slowing down by closely following the changing economic conditions, increasing costs and new living conditions.
Your policies regarding female employment as one of Turkey’s leading female executives, and we would like to know your rate of female staff in employment.
In our country, the number of female managers at strategic and decision-making points in politics, bureaucracy and private sector is almost nonexistent. We have always given the opportunity to work at strategic points in DORCE, and we continue to give women with a good education, self-confidence, developed awareness of freedom and high energy. In this age where digitalization is developing rapidly, I believe that women who have been educated with a sense of responsibility from a very young age will make timely and correct decisions. We train and employ women who can reflect their emotional gaze, humanistic solution suggestions and strong communication skills to work as managers in DORCE’s decision-making mechanism. While our rate of female employment in white collar is 40%, it is unfortunately very low in blue collar.

SUCCESS IN THESE CIRCUMSTANCES DEPENDS ON THE CAPABILITY OF COMBATING CHALLENGES AND COMPLIANCE WITH CONDITIONS
What can we see in DORCE’s new era road map? Will your growth strategy take shape aggressively or in moderation?
While we describe this period as the age of digitalization and the age of breaking, we have become a generation living the era of uncertainty. Demand and technology are constantly changing. The pandemic made the situation even worse. Companies are experiencing loss of sales, loss of market share, and decrease in profitability. While it was enough to review our strategic plans once a year until a while ago, now we do it almost weekly and daily. Success depends on your ability to cope with adversity and adapt to circumstances in this environment. Working in high energy and harmony will provide an exit from these difficult conditions. We live in a period where the human element and leadership at all levels are more prominent than ever. We need to successfully play both individual and team games at the same time, and manage the day, week, month, year, medium and long term together. In such an environment, our growth strategy in DORÇE’s new era road map will be moderately shaped by the Digitalization Strategic Plan and its Implementation, which is the inevitable part of our era.